Energy Savings: VFD vs CSV
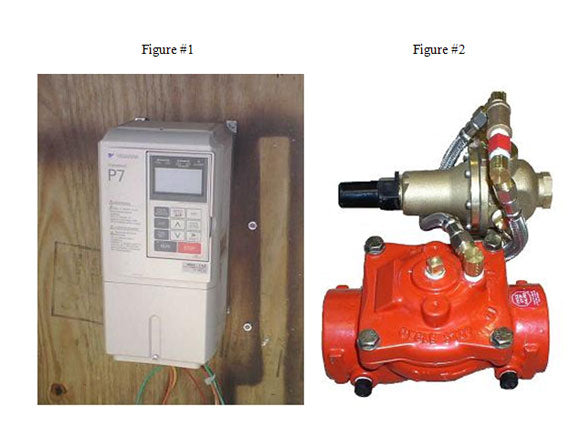
The two most common ways to produce constant pressure are Variable Frequency Drives or VFD's, and Cycle Stop Valves or CSV's. The end result is the same in that the system sees a steady or constant pressure, as the flow rates required vary from small to large. However, these two systems control the pump in completely different ways.
Variable Frequency Drives or VFD's
A VFD electronically reduces the speed or RPM of a motor to reduce the flow produced (See figure #1). A pressure sensor or transducer monitors the system, and varies the RPM of the pump to maintain a constant pressure. A VFD takes AC power from the grid, converts it to DC and charges a capacitor bank or buss. Then the VFD pulses DC to simulate AC power. In this way a VFD can pulse the DC to simulate different frequencies. Reducing the frequency or hertz reduces the RPM of the pump, which also reduces the flow, pressure, and amp draw.
Cycle Stop Valves or CSV's
A Cycle Stop Valve has no electronics and is installed on the discharge of a pump (See figure #2). The valve senses downstream pressure, and opens and closes to produce a flow rate that will maintain a constant pressure. As the pressure downstream increases, the CSV reduces the flow from the pump. As the pressure downstream decreases, the CSV increases flow from the pump. The CSV puts artificial head on the pump, to make it think it is in a deeper well, which causes the pump to produce less flow and reduces the amp draw similar to a VFD.
Energy Savings?
The phrase "green lie" has been coined to represent myth-truths and false statements which encourage people to spend money on products that are suppose to be good for the environment, but are not. Many of these things are actually harmful to the environment, and the only thing "green" about them, is coming out of your wallet.
The biggest "green lie" of all is that VFD's "save energy". When the pumps speed is reduced using a VFD, the Affinity Law states, "horse power is reduced by the cube of the RPM." Many people use this to try and show energy is being saved, by reducing the RPM. This is absolutely not true (See figure #3).
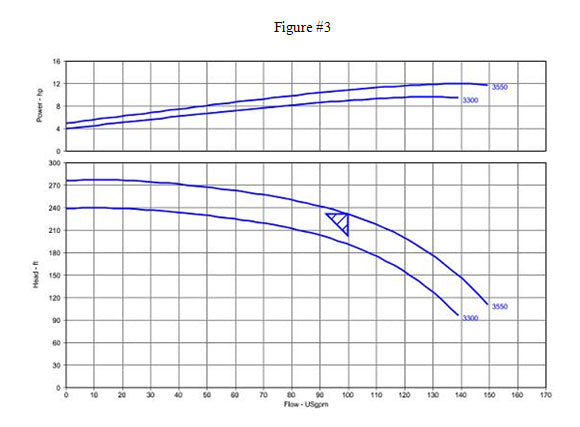
When running the pump at full speed and maximum flow, the energy used by the VFD itself, along with motor losses from the VFD's sub-standard voltage wave form, causes more energy to be used per gallon.
At reduced flow, the Affinity Law states "head is reduced by the square of the speed". Reducing the speed of a pump by 50%, which many salespeople claim to be possible, would also reduce the head produced by 75%, and the pump will not be able to lift water to the top of the well.
A reduction in speed of 15% would be a more possible scenario. This would still be a reduction in head of 28%, but might still be able to lift water to the top of the well, and produce the pressure required. Reducing the speed by 15% would reduce the horse power by 39%. If a 10 HP, 100 GPM pump could be slowed by 15% and still deliver the 100 PSI required, it would be producing 10 GPM, and drawing 6.1 horse power. This would only be 1.66 GPM per horse power, which means a VFD system is using 6 times or 600% more energy. Saving energy means reducing the energy cost per gallon of water pumped, not reducing the cost per hour to run the motor turning the pump. High flow or low, a VFD always causes more energy to be used per gallon produced.
Another "green lie" is "restricting flow with a valve is like driving a car with one foot on the gas and one on the break". The truth is that restricting the flow with a valve, causes the amps to drop almost exactly the same as when using a VFD.
The only real energy savings, comes from the system that will last the longest. It takes a lot of energy to mine, manufacture, transport, and install pumps and controls. The longer a system last, the more energy and money is saved. It is very harmful to the environment to install a system that was designed to only last a short time. Our landfills are being filled with electronic components like VFD's, and non-recyclable pumps and motors. This waste a lot of energy and natural resources, leaches heavy metals into our water supplies, and drains money out of your bank account.
Create or De-rate?
When the flow is reduced, the amps drawn by a pump controlled by a VFD, and a pump controlled by a CSV are almost the same. The difference is that a VFD creates a smaller motor from a larger one, and a CSV de-rates the motor load.
When a VFD slows down a 10 HP motor, until it is only drawing a 5 HP load, it has "created" a 5 HP motor from the 10 HP. Even though the motor is only drawing half of a 10 HP load, the harmonic content produced by the VFD increases heat in the motor. The motor must be cooled as if it were a fully loaded 5 HP, which still requires 1/2 a foot per second flow. According to the submersible motor cooling chart, a 6" motor in an 8" casing needs a minimum of 45 GPM to remain cool. So a 10 HP pump and motor in 8" casing, cannot be slowed to less than 45 GPM, or the motor will overheat and be destroyed.
The same 10 HP motor controlled by a CSV doesn't need as much flow to remain cool. This is because the 10 HP motor has been "de-rated" to a 5 HP load. When a CSV restricts a 10 HP pump, the amps can also drop to a 5 HP load. However, the motor is still spinning at 3450 RPM, and is still running on pure sinusoidal AC power, which has no harmonic content. De-rating is described in the chart for motors used in hot water applications. De-rating means a 10 HP motor that is only pulling a 5 HP load, can function properly in water up to 140 degrees. If de-rating a motor means it can remain cool in water up to 140 degrees, then it would take very little flow of 86 degree or cooler water to prevent overheating. This has been tested extensively, and we have found that 5 GPM flow is more than adequate to cool most de-rated motors. The example pump controlled with a VFD can only vary the flow from 100 GPM to 45 GPM. The same pump controlled with a CSV can safely vary the flow from 100 GPM all the way down to 5 GPM.
A smaller 30 GPM pump de-rated with a CSV, can safely vary the flow from 30 GPM all the way down to 1 GPM. This same 4" motor in 5" casing controlled with a VFD, can only reduce the flow from 30 GPM to 7 GPM.
Understanding the truth will keep you from having to suffer the consequences.